What must be done?
Consideration must be made when assessing potential risks. Check whether you need to manually handle it at all. For example, can raw materials be delivered directly to their point of use? Consider the use of mechanical handling aids, particularly for new processes. For example, can work by completed with the use of a conveyor, pallet truck or an electric powered hoist?
Dynamic vs Task-based Risk Assessment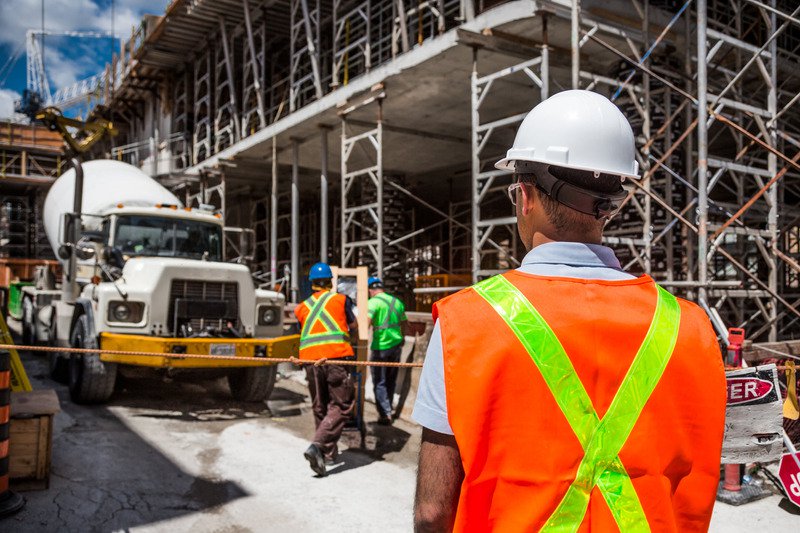
Dynamic – When a risk assessment is required on-site, a Dynamic Risk Assessment can be created. This aims to assess the risks on the spot swiftly, and doesn’t require formal documentation.
Task – A task-based risk assessment seeks to provide a more thorough breakdown of the risk and processes a manual handling task entails before it is completed. Task-based risk assessments are suitable for pre-planned repeated activities.
In all scenarios, a method of utilising manual handling aids should be pursued as this eliminates the risk altogether.
What if manual handling is unavoidable?
As set out in MOHR and the Management of Health & Safety at Work Regulations 1999 guidelines, a competent person should complete a suitable and sufficient risk assessment to identify the level of risk associated with the task and this should be applied to manual handling operations. A task-based assessment can be made via figure 1, left.
· Each box contains a guideline weight for lifting and lowering in that zone.
· If the maximum weight lifted is less than the figure given in the box, the operation is within guidelines.
Training as a control
If no other alternative method of eliminating the risk of manual handling can be found, it is vital that the correct manual handling techniques are known. |
|
The feet should be apart with one leg slightly forward to maintain balance (alongside the load, if it is on the ground). The worker should be prepared to move their feet during the lift to maintain their stability. Avoid tight clothing or unsuitable footwear, which may make this difficult. |
|
Get a good hold. Where possible, the load should be hugged as close as possible to the body. This may be better than gripping it tightly with hands only.
Start in a good posture. At the start of the lift, slight bending of the back, hips and knees is preferable to fully flexing the back (stooping) or fully flexing the hips and knees (squatting).
Don’t flex the back any further while lifting. This can happen if the legs begin to straighten before starting to raise the load. |
|
Keep the load close to the waist and keep the load close to the body for as long as possible while lifting. Keep the heaviest side of the load next to the body. If a close approach to the load is not possible, try to slide it towards the body before attempting to lift it. leg.
|
|
|