Case Studies
Health and Safety Advisory Services and ISO 9001 Support for Red Triangle Autoservices Ltd
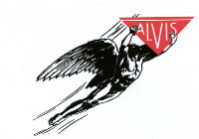
Red Triangle Autoservices Ltd
Year joined: 2019
Location: Kenilworth, Warwickshire
Consultant: Jake Sansom
About Red Triangle
In 1919, marine engineer Thomas John started a company, T.G. John Limited, in Hertford Street Coventry, making stationary engines and carburettor bodies for the newly emerging motor industry. He produced his first motor car, the 10/30 in 1920 and during the next decade went on to develop a range of high-quality sporting cars, including the famous 12/50. In 1922 the company changed its name to the Alvis Car and Engineering Company Limited and in 1928 developed the world’s first front wheel drive production car.
Alvis managed to avoid the worst of the 1930’s depression by switching production to larger, more luxurious sports cars and also having the foresight to develop an aero engine factory in anticipation of the second world war. During the same period, they were the first car company in the world to use independent front suspension and design the first all syncromesh gearbox.
After the war the aviation side of the business became the company’s core activity, producing radial engines for military and civilian use, including the power plant for the first hovercraft. Hand built cars were still made in modest numbers attracting distinguished customers such as Douglas Bader, Sir Benjamin Britain and the Duke of Edinburgh. Alvis merged with Rover in 1964 and in 1967 car production ceased with the takeover by British Leyland.
Although no longer producing cars, Alvis had an obligation to all those customers who still owned their cars and would need servicing and parts. This problem was solved when Alvis assisted the ex-directors of the car division to set up a company solely for that purpose. All the parts, drawings, technical data, and car records dating back to 1920 were transferred to Kenilworth and Red Triangle was born. Since that time Red Triangle has continued to serve Alvis owners world-wide, providing parts that include anything from a cotter pin to a complete chassis as well as restoring to ‘as new’ for customers as far away as Tokyo and California. It also provides a car servicing facility.
At Red Triangle there is a unique archive of one of the great Coventry carmakers combined with a team of people wanting to take full advantage of all that modern technology has to offer the discerning customer.
To this day, they provide an exceptional standard of service, repair, restoration, and supply of spare parts of Alvis motor cars worldwide.
What did Red Triangle Autoservices Ltd want to solve by hiring WA Management?
Support with implementing and integrated management system for health, safety and quality assisting Red Triangle to maintain ISO 9001 certification.
WA Management’s Role
What services do WA Management provide Red Triangle?
WA Management provide Red Triangle with Health and Safety Advisory Services and ISO 9001 Quality Management Systems Consultancy.
The Health and Safety Advisory Services include:
- Quarterly health and safety site audits, followed by support in the progress of addressing actions highlighted
- Bi-annual health and safety committee meetings
- Annual board report summarising key health and safety statistics
- Annual bespoke risk assessment pack
- Annual Health and Safety policy
- Access to WA Management document templates
- Regular updates to changes in safety legislation and other information via newsletter
- Unlimited advice via phone calls and e-mails
- On-going and continuous support in addressing Health & Safety issues, including addressing actions required by visiting HSE Inspectors, customer auditors, changes to legislation, and changes to activities
The ISO 9001 Quality Management Systems Consultancy includes:
- Quarterly ISO 9001 audits, followed by support in the progress of addressing actions highlighted
- Bi-annual management review meetings to review the management system business risks and set objectives
- Support with annual ISO 9001 assessments and surveillance visits against the requirements of the standard, by the appointed assessment body
- Support with the ongoing maintenance of the Management Manual, to ensure improvements in working practices relevant standards, processes, procedures and legislation changes and updates, are recorded
- Unlimited advice via phone calls and e-mails
How have WA Management added value?
After conducting a gap analysis for both Health and Safety and ISO, we have worked with Red Triangle to implement the action plan. Red Triangle are an interesting customer as part of their charm is being able to walk back in time when you visit their workshop.
WA have worked with Red Triangle to ensure that this company ethos is maintained whilst ensuring legislative compliance, a safe working environment and safe systems of work reflect modern working practices.
Red Triangle have particular risks, such as pre-war cars could come into the garage with asbestos brake pads, clutches, or headliners. WA has worked with Red Triangle to create safe systems of work improving the induction process to help screen potential asbestos containing cars and implement mitigating factors when they’re identified.